- July 2024 (1)
- December 2023 (1)
- July 2023 (7)
- June 2023 (1)
- April 2023 (1)
- March 2023 (2)
- February 2023 (3)
- January 2023 (3)
- September 2022 (7)
- August 2022 (1)
- July 2022 (1)
The Role of Thermal Interface Materials and How They Affect Performance
Jul 13, 2024Many modern electronic systems face cooling challenges that require unique thermal management strategies. Some upcoming application areas where thermal challenges are prevalent include 5G base station equipment and handsets, data center infrastructure, power management systems in vehicles, and many other areas. Fans and bulky heatsinks were often a go-to option in the past, but the form factor and noise requirements in today’s electronics are forcing designers to develop innovative strategies to transport heat away from critical components in their systems.
Although fans are still an option in many systems, designers still use heatsinks and unique enclosure designs as a path to transport heat away from high-power components. Heat then conducts into a region where natural or forced airflow can help cool the system to a lower temperature, but the main challenge is to ensure thermal contact between components, a heatsink, and/or the enclosure. Thermal interface materials can be used to provide strong thermal contact between a component or PCB, and an enclosure element or heatsink.
The challenge some designers face is in selecting the best thermal interface material for their system. These materials need to provide sufficiently high thermal conductivity to ensure high heat removal, but they also need to be integrated into an assembly process for high volume production. Designers that need to select a thermal interface material should read this guide to get an overview of their available options and why certain options are best for interfacing with heatsinks and enclosures.
TYPES OF THERMAL INTERFACE MATERIALS
There are several types of thermal interface materials, ranging from solids to viscous compounds, which are placed between a hot electronic component and a heatsink or directly to an enclosure. The differences between these materials can sometimes be difficult to see as terminology can be inconsistent, with some terms being interchangeable only by specific manufacturers. While these materials differ in terms of application and ease of use in assembly, all these materials have two common characteristics:
- They fill gaps between two surfaces such that uni- form thermal contact is
- They provide an interface with thermal conductivity reaching several W/(mK).
THERMAL GREASES, PASTES, AND GAP FILLERS
Thermal pastes, greases, and gap fillers are not always distinguished from each other, although it depends on the manufacturer of the material. Liquid-dispensable gap fillers provide the same function as pastes and greases, although they tend to have lower viscosity and are blended with pure metals, metal alloys, metal oxides, or ceramics. These thermal materials are commonly used in consumer and commercial products, such as on CPUs or in battery packs, where the goal is to dissipate heat to a heatsink or enclosure, respectively. Another area where these materials can be used is in MOSFET arrays, where die-attached pads on MOSFETs can be attached directly to a large heatsink with a thermal paste.
THERMAL EPOXY
A thermal epoxy is a much more rugged solution than thermal greases or pastes. Thermal epoxy compounds are two-part materials that begin to harden upon mixing. These materials are generally only recommended when a larger heatsink needs to be securely attached to a planar component, and a mechanical mount is unavailable or infeasible. This class of thermal interface material easily bonds to a diverse range of materials, including metals, glasses, ceramics, and plastics if the thermal expansion coefficients of the mating surfaces and hardened epoxy are similar.
SOLDER
In terms of its thermal conductivity, solder is a superior thermal interface material, but it’s scope of application is most limited. Solder should be used to connect components with an exposed die-attached pad to a corresponding pad on the PCB, which is then connected to an internal ground plane with vias. If dissipation back to the enclosure is required, a mounting screw or another thermal interface material can be used to provide a thermally conductive connection.
PHASE CHANGE MATERIALS
These materials can solidify or liquify during operation, undergoing a phase change as the component heats and cools. The advantage of these materials is that they demand latent heat to drive a phase change. These materials are viscous once liquefied, but they can be applied as solid materials during assembly. A mechanical mount is required to hold a heatsink against a component if this class of materials is used.
THERMAL TAPE OR ADHESIVE
These simple materials are strips of polyimide or other polymer material coated with a pressure-sensitive adhesive. The thermal conductivity of these materials is low compared to best-in-class thermal interface materials, but these tapes are very thin and give a simple way to create a thermal interface between a component and its heatsink. These were originally designed to provide some adhesion for heatsinks to larger semiconductor packages alongside a mechanical latch. They can also have some filler material, which is typically a ceramic with high thermal conductivity.
THERMAL PADS
Thermal pads are pre-formed in some required shape (usually a square or rectangle), and they can be cut down to fit the size of a target component and heatsink as needed. They are also flexible when applied, and they can be used on stepped surfaces on the top of some ICs. One should note that, on very rough surfaces, thermal pads may leave some leftover microscopic air gaps between the joined surfaces, but the high thermal conductivity of the best thermal pad materials compensates for any microscopic separation between the mated surfaces. Some common material systems used for thermal pads include silicone and acrylic, while graphite is used in more advanced materials.
Ohmite TGH amd TAP Series Thermal Pads
The table below shows a summary of typical thermal conductivity values seen in these materials.
Material |
Thermal Conductivity [W/(m•K)] |
Thermal pastes/greases/ fillers |
Up to ~10 |
Thermal epoxy |
0.14 (unfilled) to ~3 (filled) |
Thermal tape |
~0.5 |
Thermal pads |
~3 to ~14 |
Graphite thermal pads |
Up to ~10 (z-axis) or ~800 (in-plane) |
ASSEMBLY AND RELIABILITY OF THERMAL INTERFACE MATERIALS
Production-grade solutions should satisfy several re- quirements to ensure ease of assembly:
- Simple application and cleanliness
- Ability to fill the entire mating surface with the material
- Scalable to high volume assembly
- Adaptability to heatsinks or enclosures
- Adaptability to standard or unique footprints
The two broad classes of thermal interface materials that best satisfy these requirements are thermal pastes and thermal pads. Thermal pastes could be integrated into an automated assembly line and applied after soldering processes. Thermal pads are easier to bring into an assembly process if a vendor can provide pads in standard footprints (e.g., TO packages) or custom pad shapes.
While assembly is an important consideration in thermal interface material selection, reliability is another area to consider when selecting materials. Whereas thermal greases and compounds will harden during their lifetime, thermal pads can remain compressible and can even be replaced later as needed. Thermal paste is much more difficult to rework than a thermal pad or thermal epoxy, possibly requiring scraping or solvents that can damage the component.
When procured as a preformed pad from a vendor, thermal pads are generally a better option for prototyping than for high volume production because the pad may need to be cut down to size. However, some thermal pad vendors can provide a custom solution that fits device footprints. Some power component providers can also provide highly optimized thermal pads alongside their components to help maximize heat dissipation and reliability.
THERMAL PADS FOR POWER PRODUCTS FROM OHMITE
Among all the possible thermal interface materials on the market, thermal pads have seen some of the most innovation using advanced materials. These materials are also adaptable to a range of form factors and device footprints, giving assemblers a clean, flexible solution for attaching heatsinks to high-power components. Thermal pads are also useful for creating a thermal interface between a PCB and its enclosure, a strategy used in high-power RF products to aid heat transport.
Ohmite is best known for its broad range of power resistors, filters, and ceramic products. Ohmite also offers two types of die-cut thermal pads that match standard device footprints and their line of power resistors. By offering thermal pads with these form factor options, designers have a flexible way to apply a thermal interface material for heat transport without the need for bulky heatsinks or messy thermal pastes.
- Graphite-based pads: This material set provides high in-plane thermal conductivity as well as high in-plane electrical conductivity, allowing it to provide some EMI isolation alongside high thermal The thermal conductivity is pres- sure-sensitive, reaching 7 W/(m•K) at 700 kPa.
- Silicone-based pads: These thermal pads are a low-cost entry-level option that is competitive with other material Ohmite’s silicone pads have rated thermal conductivity of 3 W/(m•K), will easily conform to complex surfaces, and are electrically insulating.
These die-cut options eliminate the need for electronics assemblers to cut pads to size, which helps streamline production and assembly. Power products operating anywhere from DC to microwave frequencies can benefit from these two classes of thermal interface materials.
CONCLUSION
Thermal interface materials will continue to remain commonplace in advanced electronics as cooling demands persist in power systems. Newer 5G mobile devices, automotive power systems, energy systems, and aerospace systems are other areas where thermal demands can force device shutdowns, but Ohmite’s options can provide a simplified, flexible solution that easily integrates with new and existing products.
When you’re looking for thermal interface materials that are easy to apply and remain reliable over a long lifetime, look at Ohmite’s line of thermal pads. These die-cut products are available in high volume to match standard device footprints for through-hole or surface-mount components. Ohmite also offers power products, EMI products, and custom resistor assemblies for demanding applications where flexibility, form factor, and integration are critical.
Contact Ohmite today to learn more about our power resistors, EMI filters, and thermal management materials.
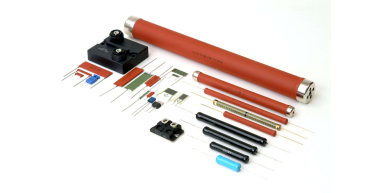
Guide to Power Resistors
Power resistors are used to dissipate energy by converting it to heat. and are designed to maintain stable performance. Call now and request a quote today!
Read More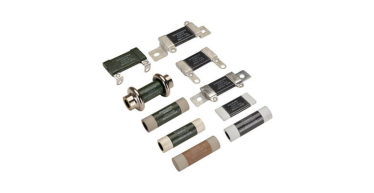
Guide to Ceramic Resistors
Ceramic Composition resistors are composed of a mixture of a finely ground insulator and conductor which is compressed into a cylindrical shape. Call now!
Read More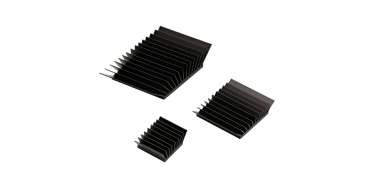
Guide to Heat Sinks
As semiconductor devices scale to smaller sizes and higher power densities, thermal management has become more challenging Call now and request a quote!
Read More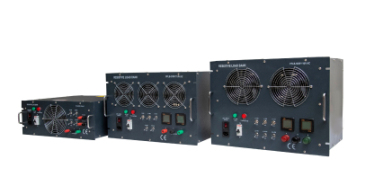
Guide to Load Banks
A load bank is a device that is intended to accurately mimic a load that a power source will see in an actual application. Call now and request a quote today!
Read More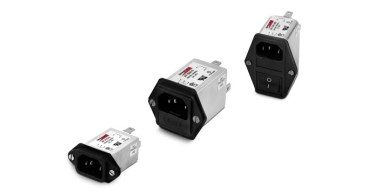
Guide to EMI Filters
To control the effects of EMI, standards are in place internationally, for commercial electronics, aerospace as well as military and space applications. Call now!
Read More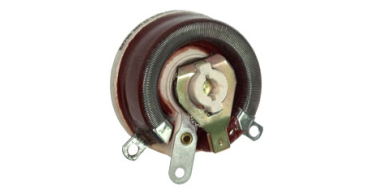
Guide to Rheostats
Rheostats, a fundamental component in electrical engineering, play a crucial role in controlling current flow and adjusting resistance in electrical circuits. Call now!
Read More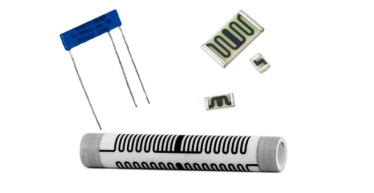
Guide to Thick Film Resistors
Thick film resistors, hailed for their versatility, durability, and wide-ranging applications, are a cornerstone of modern electronics. Call now and request a quote!
Read More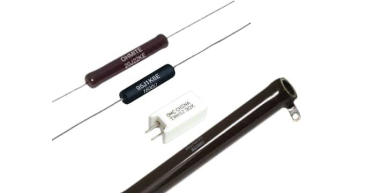
Guide to Wirewound Resistors
Thick film resistors, hailed for their versatility, durability, and wide-ranging applications, are a cornerstone of modern electronics. Call now and request a quote!
Read More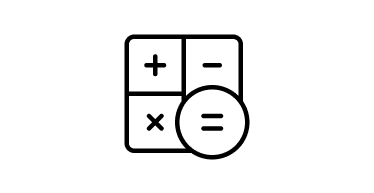
Ohms' Law Calculator
Read More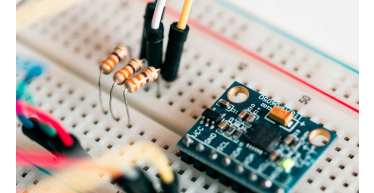
Ohm's Law 101
Ohm's Law stands as one of the fundamental principles in electrical engineering, providing a cornerstone for understanding and analyzing electrical circuits. Call now!
Read More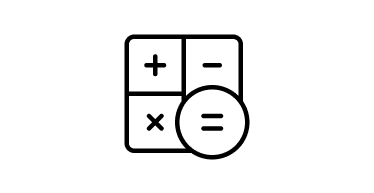
Energy Rating Calculator
Read More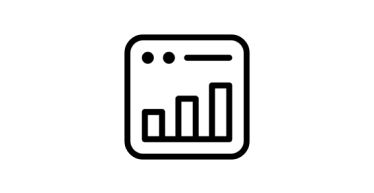
Media Library
Read More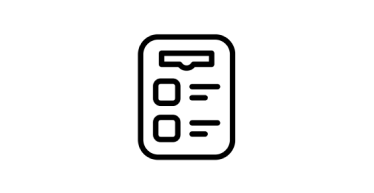
Technical Information
Read More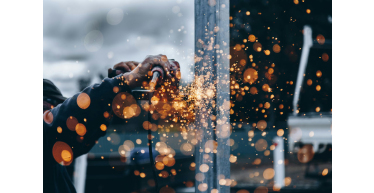
Industrial Resources
As a manufacturer of power resistors, Ohmite often creates products designed for industrial applications.
Read More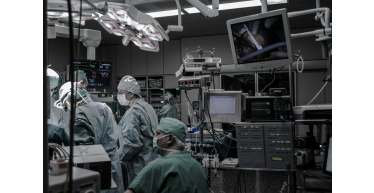
Medical Resources
As a manufacturer of power resistors, Ohmite often creates products designed for medical applications.
Read More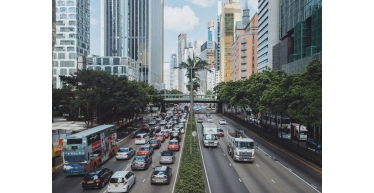
Transportation Resources
As a manufacturer of power resistors, Ohmite often creates products designed for transportation applications.
Read More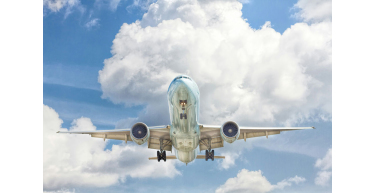
Military & Aerospace Resources
As a manufacturer of power resistors, Ohmite often creates products designed for military and aerospace applications.
Read More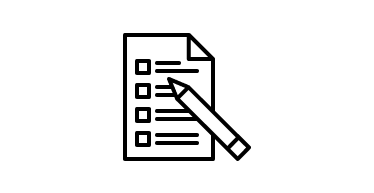